Process Manufacturing
Pumps designed to help preserve your process
The seal-less positive displacement design of Wanner Hydra-Cell Pro pumps, simple build and low maintenance qualities, offer an array of user benefits in process manufacturing applications including energy efficiency, smooth virtually pulse-free flow, high pressure capability, and the ability to handle very different types of liquids and aggressive fluids. For example, they perform reliably with corrosive acids and alkalis, complex solvents, viscous resins and abrasive slurries containing suspended solids – and they perform equally well with thin, non-lubricating liquids.
Creating real value in customers processes
Where pump users were looking to improve their industrial processes and reduce costs, Hydra-Cell Pro pump technology has successfully replaced and supplanted gear, lobe, progressing cavity, AOD, peristaltic, centrifugal, plunger, axial piston, and screw pumps. Results prove that Hydra-Cell Pro pumps deliver reliable, sustained performance over a wide range of applications in every sector of industry with unmatched performance, dependability and lower costs.
Meeting the performance criteria of API675, Hydra-Cell Pro metering pumps offers linear, repeatable, accurate steady flow. The compact pumps give the advantages of large traditional hydraulic diaphragm pumps, but at a fraction of the initial cost, spare parts costs and energy costs.
For example, at a given flow and pressure, a traditional pump with a 15kW motor can be replaced with a pump with a 5kW motor. Flow rate is varied by speed control offering turndown ratios of 10 to 1 or better.
Hydra-Cell Pro pumps offer superior performance for process manufacturing, metering and dosing:
- Ability to handle viscous fluids and shear sensitive liquids.
- Extremely low pulse flow with accurate metering, often without the need for pulsation dampeners.
- Constant flow rate, regardless of system pressure, easily controlled to within ±1% accuracy simply by controlling pump speed – with turndown ratios of 10:1 or better. Flow is steady, with little pulsation.
- Can handle solids up to 500 microns, or more. Charged and dirty liquids can be processed without need for fine filtration. System costs are reduced and maintenance is simplified.
- Pumps need little maintenance and can operate at continuous duty at high pressure.
- Pulsation is low, so dampeners may not be required for most Hydra-Cell Pro pumps.
- Most heavy-duty pumps in the Hydra-Cell Pro pump range can operate at any pressure from <1 bar up to at least 70 bar. Some models up to 170 bar.
- Seal-less design distinguishes Hydra-Cell Pro pumps from other heavy-duty pumps, and is the basis of its long service life, as many liquids commonly pumped are harmful to pump seals. Hydra-Cell Pro pumps are also tolerant of small solids, resistant to chemical and corrosive attack.
- Compact and highly efficient (80-85%), Hydra-Cell Pro pumps can be fitted with a smaller motor than would be required by many much larger heavy-duty pumps for equivalent flows and pressures.
Wanner Application Briefs
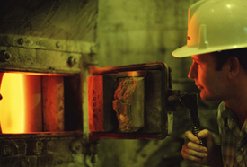
Ethylene glycol – a versatile industrial fluid
Manufacture of anti-freeze, product packaging, material reclamation and recycling are all areas where Hydra-Cell Pro pumps have been beneficial to the process. Truck-mounted Hydra-Cell Pro H25 pumps are used for pumping out reclaimed ethylene glycol from auto service centers. With their seal-less design Hydra-Cell Pro pumps handle the reclaimed fluid well, despite the presence of oils, gasoline and grit.
We can help
Wanner’s technical engineers can assist you in selecting a Hydra-Cell Pro seal-less pump to reliably handle your most challenging process liquids.
- Low NPSH due to High vapour pressure?
- Need assistance or support with NPSH in terms of system design?
- Are you replacing other pump technologies for abrasive/slurry duty application?
- Our technical engineers can assist with selecting a Hydra-Cell seal-less pump to reliably handle your process liquid.
Hydra-Cell Pro pump solutions are found in:
- Mixing
- Chemical injection
- Water treatment - PH control
- Propellant packaging
- Dispensing
- Injection of additives to oil
- Spray coating
- Gas conditioning
- Injection of lime slurries and ammonia into flue gases
- Steam temperature control with DI water
- Titanium dioxide
- Polyol
- Volatile fluids
- Foaming chemicals
- Polymers
- Lactic acid
- Animal fats
- Sugar solutions
- Soya oil
- Fish oil
- Sulfuric acid
- Nitric acid
- Halon
- Caustics
- Freon
- Pentane
- Colorings
- Fuel additives
- Flavorings
- Resins
- Slurries